Navigating around the major topics in this article may be easier by using the following links. Alternatively, a full Index is available which can be accessed by clicking here.
Introduction
Programmable systems Vs. non programmable
Basic injection system
Injection system explained - single point/multi point
Induction systems - plenums, throttle bodies
Injection system at work
Operation of the injection system
Additional information about injection
The clever stuff - lean cruise, idle control, lambda feedback etc.
Basic ignition management - wasted spark, distributor-less
Ignition in operation - timing map adjustments
2D versus 3D systems - what it means
Conversion to mapped ignition from distributor based systems
The mapping process on a rolling road
Conversion to throttle body injection from carbs or plenum
Sample maps in digestible format
MAIN INDEX
Basics of engine management
Modern engine management systems do a fine job of ensuring that engines run cleanly and efficiently in a wide variety of conditions. They are for the most part reliable and require little or no maintenance. However they seem from the outside to be fearsomely complicated systems which defy all attempts at understanding. Amidst all this apparent hokum it is easy to lose sight of the two basic functions performed by an EMS.
To meter fuel to the engine in the right quantity
To provide a spark at the right time
What is an engine management system?
An EMS is a self-contained custom-built computer which controls the running of an engine by monitoring the engine speed, load and temperature and providing the ignition spark at the right time for the prevailing conditions and metering the fuel to the engine in the exact quantity required.
There are two discrete subsystems in operation within the EMS - the fuel or injection system and the ignition system. It is possible to run an engine management system which just provides one of these subsystems, for example just the ignition system. It is much more common to use the mapped ignition within an EMS in isolation than it is to use just the injection.
What is a "map"?
Most of us have heard the term ‘mapped ignition’ and programmed or mapped injection, but may not understand what this actually is. While the engine is running, its requirements for fuel and ignition timing will vary according to certain engine conditions, the main two being engine speed and engine load. A ‘map’ is no more than a lookup table by engine speed and load, which gives the appropriate fuel or timing setting for each possible speed and load condition. There will normally be a map for the injector timings (fuel map) and a separate map for the ignition timing settings (ignition map) within the EMS.
Each map has entries for a predetermined range of engine speeds (called speed sites) and a predetermined range of engine load conditions (called load sites) which generally indicate how far open the throttle is. The EMS knows the engine speed (derived from the crank sensor or distributor pickup) and the engine load (from the Throttle Position Sensor or airflow meter) and will use these two values to ‘look-up’ the appropriate fuel and timing settings in each map.
If the current engine telemetry falls between the sites in the map then the value is interpolated between the nearest two sites. Normally there will be speed sites every 500 or so rpm and 8-16 load sites between closed and open throttle. In the example below speed sites are spaced every 1000rpm and the 8 load sites are numbered 0 to 7.
Simple example of an Ignition Map |
|
0 |
1000 |
2000 |
3000 |
4000 |
5000 |
6000 |
7000 |
8000 |
0 |
8 |
25 |
20 |
35 |
38 |
38 |
38 |
40 |
40 |
1 |
8 |
15 |
20 |
32 |
34 |
35 |
35 |
38 |
38 |
2 |
8 |
12 |
20 |
26 |
32 |
33 |
32 |
34 |
36 |
3 |
8 |
12 |
19 |
26 |
30 |
31 |
32 |
32 |
34 |
4 |
8 |
12 |
18 |
25 |
30 |
30 |
30 |
32 |
32 |
5 |
8 |
12 |
18 |
25 |
30 |
30 |
30 |
30 |
31 |
6 |
8 |
12 |
18 |
25 |
30 |
30 |
30 |
30 |
31 |
7 |
8 |
12 |
18 |
25 |
30 |
30 |
30 |
30 |
31 |
In this example the engine load increases as the load site numbers in the left column increase. If the engine were running at 3000rpm - load site 3, then the value looked up would be 26, i.e. 26 degrees of advance. If the engine were running at 3500rpm - load site 3 then the EMS would interpolate between the value for 3000rpm (26) and the value for 4000rpm (30) and calculate a value of 28 degrees.
Note how ignition advance falls as load increases. This is because cylinder filling is much better when load increases and therefore the mixture burns faster, requiring less advance.
Programmable systems vs. non-programmable systems
Most EMS fitted to production vehicles are not programmable, that is to say that the maps within the EMS which determine the fueling and ignition settings are fixed and cannot be varied by the owner. This makes good sense from a manufacturer's point of view since the engine then runs within the permitted parameters, which keeps the engine emissions and economy within known limits.
There is a burgeoning market for ‘chip-tuning’ where the chip containing the maps is replaced by another which has revised map settings providing better performance from the engine. The gains to be had here are fairly small except with turbo-charged engines where the EMS controls the boost. Chip changes on these engines can yield quite large increases in engine power. Some manufacturers go to great lengths to stop after-market tuners from decoding the maps within their EMS - with varying degrees of success. Notable EMS which are difficult if not impossible to ‘chip’ are the Rover MEMS and the Ford EECIV systems.
All after-market EMS are programmable since they have to be fitted to a variety of different engine installations in a variety of states of tune. If the map values could not be changed then the EMS would be useless for after-market applications. Some manufacturers of these systems discourage home mapping and will only allow authorized dealers to undertake the mapping.
For clarity's sake we will examine each of the two sub-systems within an EMS separately. In practice there is a great deal of interaction between the two, as both systems utilize information from the various engine sensors.
Injection system
If we ignore for a minute the actual EMS, the basic component parts of an injection system are very straightforward. Shown below is a schematic of the major parts of a multi-point injection system. Single-point injection systems are very similar, but they have only one injector and no fuel rail.
Constituent parts
Fuel tank - Holds a reservoir of fuel for the engine, is normally baffled to prevent fuel sloshing around, and the resultant fuel starvation.
Fuel filter - Since an injector pump is a positive displacement pump any foreign material ingested can stall the pump and kill it stone dead. This ‘pre-filter’ prevents rubbish from entering the pump.
Fuel pump - A high-pressure pump running at around 6 bar which supplies fuel to the injectors. The fuel pressure regulator regulates to this pressure between 3 and 4 bar (43 and 58 psi). On some installations the pump is housed inside the fuel tank with rudimentary filtration, and the fuel filter then follows in the fuel line.
Fuel line - Fuel pipe that transports the fuel from the pump to the fuel rail.
Fuel rail - A small fuel gallery from which the injectors take their fuel supply.
Injectors - Electric valves which when open allow fuel to be injected into the engine under high pressure.
Pressure regulator - A device that keeps the fuel pressure at a constant rate and returns any excess fuel to the tank.
Fuel return line - Fuel pipe which bleeds excess fuel back to the fuel tank.
Most injection systems run at quite high fuel pressure compared to a system using carburetors. Typically an injection pump will produce around 6 bar and the system will run at around 3-4 bar (43-58 psi). This is far in excess of the pressure supplied by a typical fuel pump from a non-injected system (3-10 psi). The injection system relies on a constant supply of fuel at a predetermined pressure and generally the pump runs all the time with excess fuel being returned to the tank. The map for the engine will have been derived with the fuel supply at this pressure; variations in fuel pressure will affect the quantity of fuel injected and will seriously affect the running of the engine, sometimes terminally.
Carburetors can generally cope with a short interruption to their fuel supply since they have their own reservoir of fuel in the float chamber that can be drawn from. Injection systems on the other hand cannot cope with fuel supply interruptions so it is necessary to ensure that such interruptions don’t take place. It is standard practice to baffle the fuel tank and use one-way valves to prevent fuel surge. Where space allows, a surge pot can be fitted to ensure that fuel surge doesn't’t rob the injection system of fuel at the wrong moment.
Most fuel injection pumps are gravity fed so they need to be mounted lower than the lowest point in the fuel tank. An alternative to this is to mount the pump in the fuel tank itself. Most pumps can be run completely immersed in fuel. In practice they do this anyway since inside the pump the fuel runs up and around the armature of the pump. The pump's operation is often controlled by the EMS to prevent the pump delivering fuel when the engine is not running, for example if the vehicle is involved in an accident.
The pump supplies fuel to the i njectors via a fuel rail which is a long narrow tube with a connection for each of the injectors. The fuel supply enters the rail at one end, while at the other is the fuel pressure regulator which ensures that the fuel pressure remains constant. Since the fuel pressure can affect the amount of fuel discharged in any given injector time, it is essential that this pressure is kept constant. Fuel supplied in excess of requirements is bled back to the fuel tank through the fuel return circuit which is part of the pressure regulator.
It is not uncommon for fuel pressure regulators to be tampered with to supply extra fuel pressure. This is a common dodge when an engine has been tuned and as a result needs more fuel. Since the map inside the OEM EMS cannot be varied, a certain increase in fueling can be had by upping the fuel pressure. Rising-rate fuel pressure regulators achieve the same objective. They increase fuel pressure when the engine's air demands are high, often increasing the fuel pressure in response to low vacuum in the inlet manifold, e.g. when the throttle is increased. Some EMS systems are able to cope with a small increase in airflow on their own since they know when the engine is running weak due to the Lambda feedback, and will increase fueling to compensate. This can only be achieved during steady state running so there will still be glitches in the fueling here and there.
The injectors themselves are connected to the fuel rail via a clip and ‘O’ ring which has to contain the high pressure within the fuel system. An injector is simply an electric valve or solenoid. Fuel is supplied to the injector at a known and regulated pressure, and the valve or solenoid is normally closed. Fuel is introduced or injected to the engine by firing (opening) the injector for a predetermined period of time once per engine revolution or per engine cycle. The longer the injector is held open the more fuel is introduced. This injector time is known as the ‘pulse width’ and the technique of varying fuel in this manner is known as ‘ pulse width modulation’ as it is the pulse width that is varied according to requirements. Since the fuel injected is per revolution or cycle, as engine RPM is increased, so is the number of times the injectors are fired. This has the effect of meeting the engine's requirements for fuel regardless of rpm.
Single-point injection
Single-point injection systems use a single fuel injector that injects into the inlet manifold or plenum. The fuel injected is drawn in to the cylinders by airflow in a similar way to a carburetor. Because of the variations in length and the orientation of the various branches in the inlet manifold or plenum, the fuel distribution characteristics are not ideal so economy/emissions and throttle response suffer as a result.
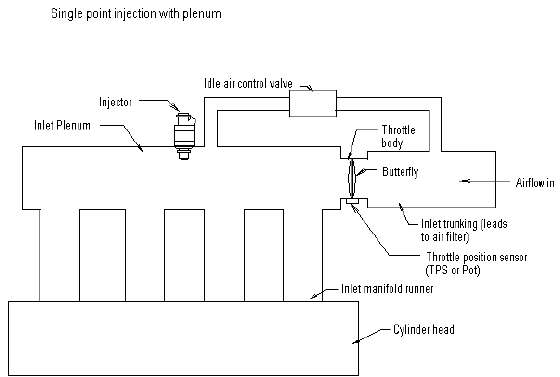 |
Although the injector position is shown in the center of the plenum, this is just for clarity. Usually the injector will be mounted on or near the throttle body where air velocity is at its highest.
Multi-point injection
Multi-point injection systems are much more common and generally have an injector per cylinder located in each individual manifold runner. This configuration gives much better control of fueling and better emissions since the fuel can be metered more closely, and there is less opportunity for the fuel spray to condense or drop out of the airflow since it is introduced as four small streams rather than one large one. The closer to the inlet valve the fuel injection takes place, the better the economy and transient throttle. Most systems use one injector per cylinder but on certain engines (notably the Rover ‘A’ series) there are only two inlet ports since two cylinders share a siamese port. In this case multi-point would mean two injectors, one per inlet port. This is still better than a single injector system.
With multi-point (or multi injector) systems there is scope for timing the injection of fuel to better suit the engine's duty cycle. If the EMS knows the relative position of each cylinder within the engine's cycle (usually from a cam-phase sensor) then it can fire the injectors at the optimum time for that cylinder. This is known as sequential injection. Sometimes the EMS will only have knowledge of the crank position rather than the duty cycle position, and in this case it can optimize for a pair of cylinders. This is known as semi-sequential or grouped injection.
Some EMS systems ignore the crank and cycle position when injecting fuel. They fire all of the injectors at the same time once per revolution, and this is known as batched injection. There is no penalty to pay power-wise when using batched injection. However, grouped and sequential injection give a slight edge on economy and transient throttle/emissions.
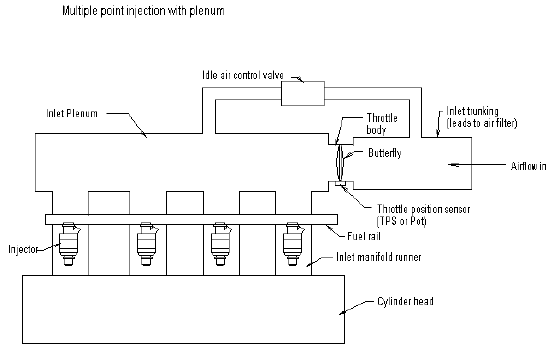 |
Induction systems
We have examined the physical hardware of the injection system itself but not actually covered the induction system. With carburetors they are one and the same thing, but with injection systems they are separate.
There are two basic types of induction systems used with injection - plenum-based systems with a single throttle body,1 and multiple throttle body systems that do not use a plenum but supply the inlet ports directly.
Plenums
A plenum is a large chamber on the engine side of the throttle body that helps to even out the pulses in the inlet tract by providing a buffer of incoming air. This in turn can help economy and emissions and also provide a longer effective inlet tract which can help mid-range torque. For single-point injection systems it is a must; for multi-point it is optional. The plenum is a convenient place to mount airflow sensors and vacuum sensors since it is at the confluence of all the inlet runners. When the engine is running, the throttle body determines how much air will flow into the plenum and therefore the engine. The plenum is generally in a condition of partial vacuum.
The EMS can maintain a good and clean idle by allowing more or less air into the plenum via a bypass valve called the Idle Air Control Valve. This together with a special idle routine in the EMS allows a perfectly controlled idle (and emissions) regardless of ambient conditions. The IACV works independently of the throttle body and bypasses its operation.
Throttle bodies
A throttle body is no more than a tube or barrel that regulates air into the engine's inlet manifold, plenum or inlet port. It is normally of tubular construction with a butterfly or throttle plate that opens and closes to regulate the airstream. Some throttle bodies have provision for mounting of fuel injectors, but others do not - it depends entirely on the application. The type of throttle body that feeds a plenum is normally a single body and it has no provision for an injector pocket. Throttle bodies are essentially like carburetors but without the float chamber or jets/venturi's. Their configuration is often similar to carburetor configurations in that they are generally available as individual throttle bodies or twinned as dual bodies.
Individual throttle bodies
Performance induction systems normally involve the fitment of individual throttle bodies for each inlet port/manifold runner. Individual bodies can be aligned precisely with the inlet ports and this can give advantages. A system that provides individual bodies to each of the inlet ports should maximize the airflow potential for each cylinder and therefore help to improve the engine's performance. Sometimes these bodies are designed to bolt straight to the cylinder head for a particular application and can be designed to taper to an exact fit on the inlet port.
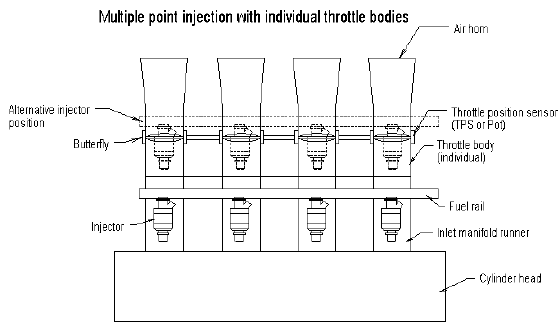 |
Dual throttle bodies
These perform the same function as the individual bodies but have two single bodies which are joined together with a fixed spacing between the individual barrels which may not be absolutely in line with the inlet ports. These are not unlike Weber DCOE or IDA carburetors in appearance. Often the difference in alignment between barrels and ports is negligible and so does not affect the performance of the engine. A set of dual throttle bodies is normally substantially cheaper than a set of individual throttle bodies. Dual bodies can often be fitted directly in the place of existing carburetors utilizing the same manifold, air filters etc., which can bring down the costs considerably.
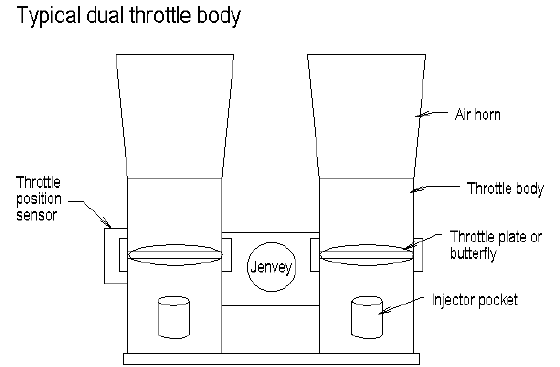 |
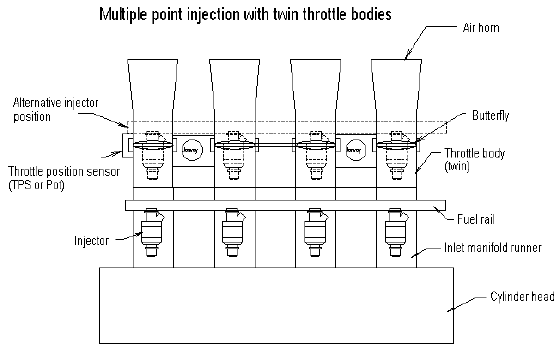 |
The injection system at work
The EMS needs to know a number of things about the engine's condition in order for the fueling to be metered correctly. During normal running these boil down to the engine speed and the throttle or load position. Generally this information is relayed to the EMS by sensors or triggers on the engine. The engine speed is determined by either a crank position sensor (which gives crank position from which speed can be derived) or a trigger of some kind in the distributor (if fitted). Engine load can be determined using a number of different methods.
Engine speed and position
Engine speed and position is normally monitored by one of the following two methods:
Crank Sensor
This is now the most common method of determining engine speed on a modern engine. It is comprised of a disk mounted on or machined into the flywheel/front pulley that turns with the engine. The disk has a certain number of teeth around its circumference and a fixed closely mounted induction sensor that pulses when it encounters a tooth. There is generally a pattern of missing teeth so that the EMS can tell exactly the crank position as well as speed. Although the EMS knows the engine's crank position from this sensor, it does not know the engine's cycle position. In a four-stroke engine the engine cycle involves two complete revolutions of the engine with the piston at TDC twice during the cycle. One of these times the cylinder is ready to fire; the other time is at the end of the exhaust stroke. A crank sensor alone can only indicate that the piston is at TDC, it cannot know which of the two cycles positions the engine is at.
Distributor pickup
Some older systems and many after-market systems use a distributor pickup to determine engine speed. The type of distributor used is normally Hall effect, magnetic reluctor or Optronic and has no in-built advance mechanism. A distributor-based system has the advantage of mechanical awareness of the engine's cycle position as well as the crank position. By attaching an inductive pickup to spark plug lead number '1', the EMS can be made aware of the engine's cycle position. This can simplify the implementation of the ignition system for an after-market conversion and provide the feedback necessary for sequential injection
Engine load
Engine load is normally determined by one of the following methods:
Throttle Position Sensor
This is the most common engine load sensor especially on after market systems. A TPS is a small potentiometer (or ‘throttle pot’) which is connected directly to the throttle shaft and turns with it. It returns a value to the EMS depending on the throttle position. TPS sensors are normally used on performance engines where airflow sensors might become confused because of pulses in the inlet tract. Because they do not measure airflow but simply give a throttle position, airflow is assumed to be constant for any given engine speed and throttle position. If the engine is further modified, the airflow characteristics may change and the engine may need re-mapping. EMS systems that use direct airflow measurement can often cope with changes more effectively and can alter the fueling to suit without a re-mapping session.
Air metering flap
Another way of determining the engine load is to measure the airflow into the engine and this can be done using a flap which is deflected by incoming air. This is commonly known as an airflow meter. These are common on older injection systems, but can be confused by reverse pulses in the inlet tract when more extreme cams are used and can be restrictive to the inlet airflow.
Manifold Air Pressure sensor
These measure the vacuum or air pressure in the inlet manifold which in turn gives an indication of load. They are more commonly used on turbo charged engines to give an indication of boost level. This is often referred to as a MAP sensor, although not to be confused with a 'map'.
Hot wire
This approach uses a heated platinum wire and measures the current required to keep it at a particular temperature. As air passes over the wire it cools it down, so the more air that passes, the greater the cooling effect and therefore the greater the current. The hot wire system can be also be confused by reverse pulses when more extreme cams are used.
Operation of the system
The way the EMS manages injection is quite simple - the sensors and triggers on the engine relay information to the EMS about engine speed and load. The EMS uses these to extract the appropriate injector time from the injection map and then fires the injector(s) for this length of time. If the system uses batched injection then all of the injectors are fired at the same time once per engine revolution. With grouped injection the injectors are grouped together in pairs which are fired at an optimal point in the engine's cycle which best suits those two cylinders, again once per revolution. Where the engine sensors are able to determine the engine's cycle position (usually from a cam phase sensor) it is possible to fire the injectors at the optimum time for each individual cylinder. This is known as sequential injection. Rather than firing once per revolution, each injector is fired for twice the pulse width at the optimum time in the engine's cycle, e.g. immediately before the inlet valve opens. There are minor benefits in economy and emissions to be had from using sequential or grouped injection, but power-wise there is little or no difference.
As we can see, information from these two main input sources allows the EMS to orchestrate the engine's fueling so that the engine runs happily in normal conditions. There are times however when the engine is not running under these ideal conditions and it is at these times that other vital feedback is required to allow the EMS to run the engine properly. Generally under these conditions the EMS makes adjustments or corrections to the fuel map according to what it knows about the prevailing conditions. The main environmental conditions that are monitored by the EMS are as follows:
Engine temperature
When an engine starts from cold it is well below its normal operating temperature. This causes some of the fuel injected into the engine to condense rather than atomizing and being drawn in efficiently. Combustion chamber temperatures are also low which leads to incomplete and slow combustion. These effects cause the engine to run weak and require extra fuel to be supplied to compensate. In a conventional system the 'choke' on the carburetor performs this function. On an injection system a coolant temperature sensor provides the EMS with the engine's temperature and enables it to ‘correct’ the fueling. This correction involves adding a percentage of extra fuel according to a predetermined correction profile by temperature, up to the normal operating temperature of the engine. The amount of extra fuel will vary from engine to engine and according to the engine's temperature and rpm, since the effects of condensing are less when air speeds are higher.
Air temperature
When air temperatures are high, the density of the air being inducted falls off, thereby lessening the volume of oxygen available for combustion. If the fuel that is injected remains constant then the mixture will become too rich. To compensate for this the EMS applies a correction to the base map according to a predetermined correction profile. As the air temperature rises so air density will continue to fall and hence the fueling will be reduced. Information about air temperature is relayed to the EMS by an air temperature sensor. To some extent airflow meters can compensate for lower density air since depending on their type they may show less volume of air inducted, and this will cause the EMS to adjust the fueling accordingly.
Battery voltage
If the voltage of the vehicle's battery varies then it is likely that the time taken to open the injectors will vary. Since the EMS times the overall injector pulse, if the injector takes longer to open then the time it remains open will be that much shorter and therefore the fuel introduced to the engine will be correspondingly less. Some EMS have a correction of injector times applied to the base map for variations in voltage; the corrections are usually small but during shorter injector times (idle and cruise) they can be very significant to the efficient running of the engine.
Mixture strength
Some EMS make use of a Lambda sensor which sits in the exhaust of an engine and measures the air/fuel ratio or strength of the mixture while the engine is running. During conditions of steady state running, the EMS is able to tell from this sensor whether the mixture is rich or lean, and can make real-time adjustments to bring the mixture back to 'chemically correct'. This generally happens only when in steady state, e.g. at idle or when cruising, and is known as ‘closed loop running’. Over a period of time the EMS can ‘learn’ whether the mixture is rich or lean and make long term adjustments.
Knock sensing
A knock sensor is an acoustic sensor that listens for pre-ignition - more commonly known as knocking or pinking/pinging. It is most likely eradicated by adjusting the timing but there are circumstances where the mixture needs trimming as well. When this is detected the EMS is able to adjust the fueling if required in order to help eradicate the problem.
Other Corrections
There are some additional corrections that the EMS can apply intuitively by examining changes in state or other derived conditions. The most common are:
Acceleration fueling
When the throttle is opened suddenly there is generally a weakening affect on the induction since air is lighter than fuel and is drawn in more rapidly. Weakening on throttle opening transients is also caused by the fact that the fuel has already been injected and the inlet valve is open before changes in the inlet manifold can take place due to a throttle change. This is only a transitory effect but it can cause the engine to stumble or stutter on initial acceleration. To counteract this tendency the EMS can keep track of sudden changes in throttle position or load and add a percentage of extra fuel when this happens. The extra fuel is only added for a short period and is then decayed over another short period. This is normally a number of engine revolutions rather than a period of time. This is known as ‘accelerator clamp’.
Deceleration fueling
When the throttle is closed suddenly and the engine is being overdriven, the hydrocarbon levels in the exhaust can rise dramatically. It is also possible for un-burnt fuel to ignite in the exhaust system producing the characteristic popping on overrun. To overcome this some EMS will either reduce the fuel to the engine on overrun or in some cases cut it off all together.
Cranking fueling
When the engine is actually being started, the cranking speed is quite low (150-200rpm or thereabouts). This means that the airspeed in the inlet ports is minimal and may not be sufficient to atomize and draw in all the fuel from the injectors. It is normally necessary to add some extra fuel while cranking to overcome this drawback. The amount of extra fuel to be added can be built into the base map at speed site zero, but it is more usual to have a correction to the base map which is a percentage of extra fuel to be added when cranking. This extra fueling can also vary with engine temperature so the correction is normally in a table for each of a range of engine temperatures. This correction normally decays quite quickly once the engine has fired since it is only required at low crank speeds. The percentage of extra fuel required will vary from engine to engine. This is often known as startup correction or cranking correction.
Additional information
There is some additional information about injection systems which does not fit neatly into any particular category but is nonetheless useful information. This is detailed below:
Injector position
The position of the injector in the inlet tract has a noticeable affect on the way the engine runs. It can affect economy, transient throttle and power output. It is generally accepted that injector positioning close to the inlet port gives good economy, transient throttle and idle, together with good emissions, and that injector positions further back in the inlet tract improve power at the expense of these criteria. Ultimately for the best power output the injector should be sited as far back as possible, i.e. in the trumpet or air-horn. Sitting the injectors here does give a big problem at low throttle openings and low rpm since the fuel hits the butterfly. It can also cause fuel to be bounced out of the trumpet by the shock waves in the inlet.
Dual injector systems
Dual injector systems attempt to exploit the benefits of the close-to-port injector while also gaining from the power increase to be had from having the injector in the trumpet. The way this is done is to fit two injectors, one close to the inlet port and one in the trumpet. The EMS controls these two injectors using the near injector for part throttle, low rpm and transient and switching to the second trumpet mounted injector when the engine is at WOT (Wide Open Throttle). Some systems switch from one injector to the other immediately a certain set of conditions is reached, while other system go 50/50 between the injectors or grade one injector's usage down while ramping the other's up. This system if implemented properly gives the best of both worlds.
Twin injector systems
Twin injector systems are normally used when the size of injector required would be very large and might affect the metering and atomization capabilities at low rpm and idle, typically on a turbo charged engine where fueling requirements vary enormously from transient to wide open throttle. The fuel can be metered through one injector when requirements are low, and through both when requirements grow exponentially, or it can be metered through both at all times. Often a second set of injectors are fitted by after-market tuners whose modifications may require fueling beyond the capacity of the current injectors. This is most likely to happen in turbo or supercharged installations.
Injector duty cycle
In order to inject a fuel into the engine, the injector is opened for a period of time, known as the pulse width, this time is always the same for a given quantity of fuel, regardless of engine speed. As engine rpm increases, the time available per revolution to fire the injector is less - at 6000rpm the time available is exactly half the time at available at 3000rpm. As this injection opportunity gets progressively smaller the injectors are required to fire much more frequently. This can result in the injector being open almost all the time. When the injection system used is sequential, the requirement is to be able to deliver the fuel at a time when the inlet valve is closed. This further reduces the injectors' opportunity to fire.
The percentage of time that the injector is open is known as the ‘duty cycle’ and this represents the relationship between the time the injector is closed, measured against the time it is open. If the duty cycle goes above 90per cent anywhere in the rev band (i.e. the injector is open for more 90per cent of the time) then the injector capacity is being reached and the engine may require larger injectors. These will discharge more fuel in a given period of time which means the injector times can be decreased, bringing the duty cycle into acceptable limits. Unfortunately this also means that the engine will need re-mapping to suit the new larger injectors or the mixture will be hopelessly rich.
Some EMS have a scaling factor which represents the relationship between the map figure units and the pulse width. By varying this, the whole map can be scaled up or down for different sized injectors. This is not a perfect way of coping with a change of injector size because the time taken to open the injector is the same and the scale factor affects this too. However it will get 95per cent of the way there when changing injector sizes.
Injector sizing
In order to size injectors for a given engine it is important to know their discharge rate. From this and an approximation of the engine's potential rpm, potential peak power and torque an estimate can be made and an appropriately sized injector chosen. It is better to err on the large side just in case you reach the injector capacity while mapping and have to start from scratch. Larger injectors have a couple of disadvantages in that the granularity of adjustment is larger and the atomization of fuel is poorer with a larger orifice.
The clever stuff
As well as the normal running of the engine and administering of fuel according to the map settings some EMS can perform some rather clever tricks which can help with smooth running, performance, economy and emissions. Most of these involve a feedback loop of some kind from the various engine sensors and involve assumptions about the way in which the engine is being used.
Idle control
When an engine is idling and at normal temperature, its airflow requirements are fairly constant and the ignition advance and the idle can be set at a constant rate. If any of the environmental conditions vary, e.g. engine temperature, air density etc. then the required airflow, ignition advance and fueling may need to vary in order to allow the engine to idle. In a carburetor-based system there is often a fast idle that is set when the engine is cold and the choke is operating, which raises the idle speed to prevent stalling. Most EMS systems use an idle control system for when the engine is idling. An idle air control valve (IACV) allows the air to the engine to be metered independently of the throttle butterfly. If the rpm falls below acceptable limits then more air is bled into the engine. If the rpm goes beyond an upper limit then less air is bled in. Together with fueling and ignition variation, this system maintains a rock steady idle with acceptable emissions in all conditions whether the engine is hot or cold.
Closed loop running
In order to minimize emissions and also to ensure that the exhaust catalyst function is optimized, many EMS have special routines coded within them to exploit situations where the engine is not under full load conditions, i.e. when cruising on a partial throttle. A large proportion of motorway driving is done under these conditions especially when cruise control is fitted to the car. The EMS enters a state know as ‘closed-loop running’ when the throttle position and engine speed are more or less constant. This indicates a cruising condition. In this state the feedback from the Lambda sensor and knock sensor are used to trim the fueling and advance to give the best possible economy and efficiency. When running in the closed loop the EMS will progressively lean off the mixture until the feedback from the sensors indicate that it is approaching detonation and will hold the mixture just before this point until the engine telemetry tells it that the engine is no longer cruising. This is known as ‘lean cruise’ and is only possible if the EMS has Lambda and knock sensing. On non-catalyst cars, lean cruise can go even further with the leaning of the mixture to save more fuel. However the mixture has to be kept near stichomythic for the catalyst to work effectively.
Open loop
This is not really a clever mode of operation but included here for completeness. At full throttle, the Lambda (oxygen) sensor is almost always ignored. This is called open loop running. In this situation, the EMS bases its decisions entirely on the information contained within the maps. This characteristic means that self-learning cannot be used (or relied upon) to cater for the increased full-throttle fuel supply required for engine mods that increase power and therefore airflow. However, self-learning often does help in the changed requirements occurring in part-throttle conditions.
The reason the Lambda sensor is normally ignored is that it can only indicate mixture strength through quite a narrow band of air/fuels ratios and it is likely that its feedback will be swamped by the fueling when accelerating and at wide open throttle. Some systems fit a wide-band Lambda sensor which can report on the mixture strength over a wider band of settings and can therefore give useful feedback even when the engine is at wide open throttle and in the acceleration fueling band of operation. This can allow the EMS to learn about mixture strength and monitor/adjust the fueling even in these extreme circumstances.
Most EMS also use map information only for ignition timing in this situation. However, a few EMS use the feedback from the knock sensor in a self-learning approach similar to that done with the lambda sensor on the injection system.
Self learning
In addition to closed loop running the lambda sensor is also used in some EMS as part of a self-learning system. For example if the fuel pressure regulator in your car is working incorrectly and supplying less pressure than it should, the mixture will probably be a bit lean. The Lambda sensor feeds this back to the EMS which then richens up the fueling. If this is happening consistently then the EMS knows that the mixtures are always a bit lean and will permanently richen up the mixture. It has learned that the mixture is lean and that richer mixtures are needed, and will always run this correction. If the pressure regulator is subsequently replaced or repaired, the EMS will then gradually re-learn the new requirements. This self-learning process occurs in most manufacturers EMS but is rarer in after-market systems. Self-learning of mixture strength is totally dependent on the Lambda sensor.
Injector cutting
In the interest of economy and low emissions some EMS can switch off the injectors completely when the engine is being overdriven, for example when you lift off the throttle totally. The injectors resume normal service when engine revs drop to around 500rpm above idle. If you watch the tachometer closely you can see the needle lift a bit when the injectors resume their flow. This is more usual on manufacturers EMS than after-market ones.
Self Diagnosis
Many engine management systems also have a 'self-diagnosis' ability. This allows you to probe the EMS using a PC and it will tell you if it has developed a problem. For example if the engine temperature sensor wire is broken the EMS will report that there is no input from it. Some EMS will communicate faults via fault codes or flashing lights, while others require a diagnostic computer to be attached. Again, this is more common with OE management systems.
Traction-control, cruise control and drive-by-wire
There are areas of an EMS that can interact with other systems on the vehicle such as traction-control and cruise-control. In the more sophisticated systems a separate traction-control unit can communicate with the EMS to invoke a variable rev limit that cuts engine torque if it senses that traction is being lost. Normally this is done by using a soft-cut rev limiter which is invoked at will. On other systems the EMS is actually able to back off the throttle.
Some recent EMS that are installed alongside intelligent or adaptive transmissions are designed to co-operate with the transmission. A common practice is ‘drive-by-wire’ where there is no direct connection between the accelerator and the throttle butterfly. Instead, a stepper motor controlled by the EMS applies the throttle. This makes it easy for the cruise-control or adaptive transmission to orchestrate the engine as it sees fit. A traction-control system might back off the throttle in response to lost traction. A cruise-control system will both apply and back-off the throttle to maintain its programmed speed.
Rev limiting
Most EMS systems implement a rev limiter, some allow a soft-cut where the engine selectively misfires followed by a hard-cut a little higher up where the engine simply stonewalls. Some limiters cut off all fuel at the prescribed engine speed, withholding it until you're 500rpm below the limit. Other rev limiters cut off the spark (or injectors) of individual cylinders one after the other, progressively cutting more and more until the hard-cut limit is reached so that you can barely feel that you have reached the maximum allowable rpm. These soft limiters mean that the car can be used right to the rev limit without a worry. Normally the EMS will maintain the tach signal consistently to ensure that it doesn't’t go crazy. Often the rev limiting is coupled with a shift light that warns the driver that the rev limiter is about to operate and he should change up a gear. With batched and grouped injection systems, selective cutting of fuel can be dangerous since the fuel is not injected at the optimum time for each cylinder and it is quite possible for a cylinder to induct only a partial charge of fuel which could result in detonation and resulting damage.
Tach and tell-tale
Most EMS systems drive the tachometer (rev counter) directly which allows them to maintain the tach reading even when the rev limiter is invoked. Some after market EMS also provide a tell-tale facility that will flick the tach needle to the highest rpm attained during its previous use.
Fan control
EMS systems as fitted to production cars can also control other aspects of the engine's systems. It is very common for the EMS to control the cooling fan, switching it on and off as required.
Water injection
Some EMS systems can control a secondary water injection system that is used in forced induction engines to cool the incoming charge and to prevent detonation. They may also be capable of controlling water-cooling sprays onto charge coolers that help to cool the air inducted into the engine.
Nitrous oxide injection
Nitrous Oxide (NO2) is a gas that contains much more oxygen than air does on a weight by weight basis; NO2 is often used to boost the power of an engine. It is injected with extra fuel and effectively increases the amount of fuel and oxygen inducted into the engine with similar affects to turbo charging or supercharging. Some EMS systems have provision for controlling the nitrous injection and the extra fuel requirements.
Turbo Anti-lag
One of the problems associated with turbo charged engines is the time taken for the turbocharger to spin up to speed and provide boost. When the engine is accelerating the turbocharger is spinning rapidly and making boost, but when the gear change takes place or when the throttle is lifted, the turbo will slow down and boost will drop off. The boost takes some time to get going again which means that the engine will drop off the power band. This time between planting the accelerator and boost becoming available is called ‘turbo-lag’ because the turbo lags behind the accelerator. Some EMS systems are able to minimize this when the engine is backing off by firing the mixture in the cylinder when the exhaust valve is open. The burning gases expand rapidly and exit the exhaust valve at high speed instead of trying to push the piston down. The ‘kick’ from the exhaust keeps the turbo speed up and minimizes lag. Generally this is only done when the engine is being backed off, so although the cylinder doesn't fire properly, the net effect on the vehicle's performance is marginal. However the effect on the turbo spin speed is quite marked. Firing the cylinder when the exhaust valve is open also provides those spectacular backfiring, banging and exhaust-flaming antics seen so frequently in the WRC turbo cars.
Auxiliary device outputs and control
Since the EMS knows so much about engine conditions, it is often useful to be able to harness the information to drive or run other systems associated with the engine. Many EMS do provide outputs or feeds which enable the more enterprising to use the EMS information to make improvements to other aspects of the car. For example EMS information can be used to switch an alternator off at high rpm and thereby minimize the parasitic losses associated when the power is needed most, or to modulate the cooling fan at times when the engine's power is needed.
Feature disclaimer
There are many other features and options within after-market EMS which may or may not be used with a particular installation. Some are obscure and are designed to meet the particular requirements of a certain piece of injection hardware or another co-operating device. It would be madness to attempt to list all of this rich cornucopia of functionality for the many and varied EMS available. Suffice it to say that the features listed above cope with 99.99 percent of what is required from a management system and in the interests of keeping it simple I will elaborate no further.
Ignition management
There are two types of ignition management system, those triggered by a distributor and those triggered from a crank position sensor, often called distributor-less. The adoption of the term distributor-less can be misleading since many crank-triggered systems still use a distributor cap and rotor arm to dispatch the spark to the appropriate cylinder. With these systems a crank sensor and not the distributor does the triggering to the EMS.
Distributor based systems
Distributor-based systems use a conventional distributor to trigger the EMS but the distributor will have no in-built advance mechanism. Typically the trigger will come well before the ignition point and the EMS will work out when to fire the ignition coil. The spark is then carried to the appropriate cylinder in the conventional way via the rotor arm and HT leads.
Crank trigger based
Since crank-triggered systems only know the engine position and not the cycle position they need a way of ensuring that the correct cylinder receives the spark. There are three common ways of achieving this.
The first is to use a conventional distributor cap and rotor arm that is normally attached to the end of one of the camshafts and routes the spark to the appropriate cylinder.
The second method is to use two coils that are paired to fire cylinders 1 & 4 and 2 & 3 respectively. When one of the coils fires it sends the spark to both of its cylinders. One of these will be on the firing stroke and will fire normally, the other will be on the scavenge part of the cycle (exhaust stroke) where the spark will be wasted, for this reason these systems are known generically as ‘wasted spark’.
The third method is to use an additional sensor on one of the camshafts so that the EMS is aware of the engine's cycle position and can fire the appropriate cylinder at the correct time using individual coils for each cylinder.
Distributor triggered
This type of arrangement is used with early EMS such as the Ford ESC system. It is also popular for after-market applications since it enables the installer maximum re-use of existing components. Any inaccuracies in the distributor manufacture are reflected in the distribution of timing between the cylinders, since the spark is always relative to the trigger points given by the distributor. Typically the distributor will trigger four times per engine cycle i.e. twice per engine revolution.
The distributor will have no advance mechanism installed or will have the advance mechanism rendered inoperative since the EMS provides for the engine's needs.
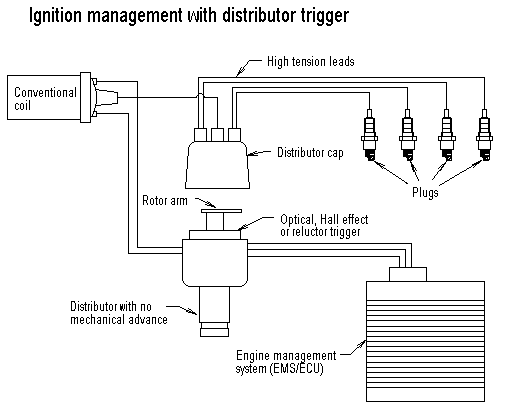 |
How it works
Normally the distributor will ‘trigger’ at around 65-70 degrees before TDC since this is greater than the expected maximum advance. The EMS will then look up the ignition map to calculate the appropriate timing figure for the engine's speed and load, then using the engine's speed as a factor will calculate how long to wait before firing the spark. The initial trigger point must be at least the maximum advance figure plus a few degrees latency to allow the microprocessor to do its work.
The conventional distributor cap and rotor arm ensure that the spark goes to the correct cylinder since the EMS will produce a spark every time the distributor pulses. Given that the system is given a pulse from the distributor for each of the appropriate cylinders, it would not be difficult to use the triggering information for the injection system to provide sequential injection. However it would be necessary to have additional feedback to determine which of the pulses belonged to cylinder number '1'. I have seen this done by attaching an inductive pickup onto number '1' spark plug lead.
Crank triggered
This type of system is a halfway house toward a totally distributor-less system. Only the distributor cap and rotor arm are retained; the rest of the distributor is not present. Typically the rotor arm is installed on the end of the camshaft and the distributor cap is bolted over. It has most of the advantages of a totally distributor-less system in that it uses a crank sensor. The EMS however is unaware of the engine's cycle position so it can only provide batched or grouped injection.
The Rover ‘K’ series MEMS uses this system for its basic implementation and therefore can only provide grouped injection. Some of the Vauxhall engines use this system also. It is a very popular and low-cost way of implementing managed ignition. It allows the manufacturer to re-use many of the constituent parts of earlier distributor-based systems.
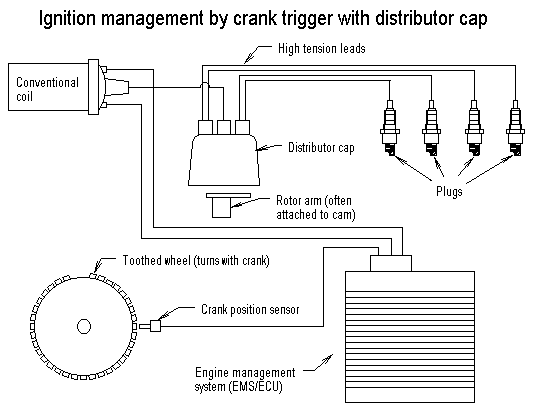 |
How it works
The EMS is aware of the TDC position from the crank sensor and by counting teeth can tell exactly what the engine position is at any time. It uses this information together with the information from the throttle position sensor/MAP sensor to look up the appropriate ignition timing settings from the ignition map. It is then able to determine exactly when to fire the coil. The coil is fired twice per engine revolution at exactly opposite positions in the engine's rotation because when cylinder 1 & 4 are at TDC, cylinders 2 & 3 are at BDC and vice versa. The spark is then routed to the appropriate cylinder by the rotor arm and cap.
Wasted Spark
This type of system does away with the distributor altogether. It uses the crank sensor to indicate where TDC is and then uses the signals from the sensor and the map information to determine when to fire the spark (twice per revolution). It groups the signals to two separate coils which provide the spark to pairs of cylinders that are at the same relative crank position. One of these cylinders will be on the firing stroke and will ignite; the other will be in the scavenge stroke and therefore the spark will be ‘wasted’. This is why these systems are known generically as ‘ wasted spark’ systems. In practice the coils are usually double-ended with a high-tension lead running from either end to each of the cylinders in the pairing.
The Ford Zetec and Vauxhall 16V engines use this type of system.
There are variations to the wasted spark system which uses individual coils for each cylinder that are paired together in parallel rather than using a pair of coils, each serving two cylinders.
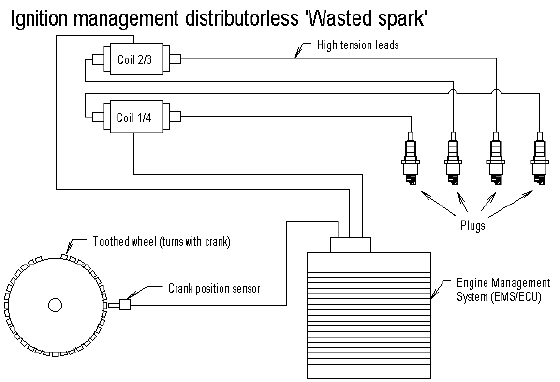 |
How it works
The EMS is aware of the TDC position from the crank sensor and by counting teeth can tell exactly where the engine position is at any time. It uses this information together with the information from the throttle position sensor/MAP sensor to look up the appropriate ignition timing settings from the ignition map. It is then able to determine exactly when to fire the coils. Each coil is fired once per engine revolution at exactly opposite positions in the engine's rotation, because when cylinder 1 & 4 are at TDC, cylinders 2 & 3 are at BDC and vice versa. The spark travels to both of the paired cylinders.
Cam Sensor
This type of system is similar to the ‘wasted spark’ system in that it is distributor-less and multiple coil. It has a cam phase sensor in addition to the crank sensor which allows the EMS to determine where in the engine's cycle each individual cylinder is. There is a discrete coil per cylinder and the EMS is then able to fire the appropriate coil.
The cam phase sensor can also be used by the injection system to provide proper sequential injection. The Rover MEMS as fitted to the VVC engine uses this kind of system, but just uses two coils as per the wasted spark set-up. The cam phase sensor is also used by the EMS to help drive the VVC mechanism. The EMS on the Subaru Imprezza uses this type of system.
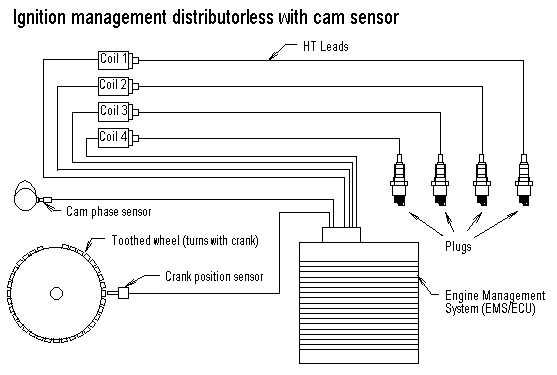 |
How it works
The EMS is aware of the TDC position from the crank sensor and by counting teeth can tell exactly where the engine position is at any time. It is also aware of the engine's cycle position from the cam phase sensor. It uses this information together with the information from the throttle position sensor/MAP sensor to look up the appropriate ignition timing settings from the ignition map. Using the crank and cam position sensors it is then able to determine exactly when to fire each individual coil since it knows which cylinder is at the firing position of the cycle. Each cylinder' s individual coil is fired once per engine cycle at exactly the appropriate time. The spark is routed directly to the appropriate cylinder.
Timing adjustments
In the normal course of events, with the engine operating at the correct temperature in defined conditions, the EMS will use load and engine speed to derive the correct ignition timing from the map. However there are circumstances under which the EMS may need to vary the ignition timing. These normally boil down to four circumstances, engine/coolant temperature, air temperature, knocking and start-up.
Engine temperature
When the engine temperature is low the burn times within the cylinders are longer than with a fully warmed-up engine and the ignition timing will normally need to be advanced a little to adjust. The EMS usually has a small map of ignition timing adjustments graded by engine temperature that are added to the base timing figures. The engine temperature information is relayed to the EMS by an engine temperature sensor attached to the engine.
Air temperature
When air temperature varies, so does burn time of the inducted mixture since it is less dense. Again, a small map of ignition adjustments graded by air temperature is added to the base timing figures. The engine temperature information is relayed to the EMS by an air temperature sensor located near to the air inlet.
Knock sensing
There may be times during the operation of the engine, even after adjustments have been applied, when the timing calculated does not meet the engine's requirements. Sometimes this may result in ‘pinking’ (a.k.a. ‘knocking’ or ‘pinging’) where the mixture burns so fast that it meets the piston just before TDC, while it is still on the compression stroke - rather than meeting the piston just after TDC on the power stroke. This is very harmful to the engine. Some EMS have an acoustic sensor called a ‘knock sensor’ which listens for knocking and will inform the EMS when this occurs. The EMS is then able to make adjustments to the timing to prevent the occurrence of knocking.
Start-up or cranking
When starting an engine, its effective rpm is quite low - around 200rpm or so. If the ignition timing used at idle is set to around 25 degrees (which is about average for a mapped engine) the chances are that the piston will hit the ignited mixture while still on the compression stroke. This will have the effect of pushing the piston down against its normal rotation, effectively this is ‘knocking’ at cranking speeds. This is known as ‘kicking back’ and is normally characterized by the starter motor ‘straining’ and slowing right down, this makes the engine difficult to start and can easily destroy a starter motor in short order.
This is a common problem on engines equipped with mechanical ignition systems and more extreme cams, since the engine needs plenty of ignition advance at idle to run properly. Unfortunately this extra advance can also cause ‘kick back’ and there is no way with a mechanical system to differentiate the timing between cranking and idle.
EMS solve this problem by having a separate timing value for cranking/start-up which is normally set to around 5-8 degrees. This is low enough to prevent kick-back but is high enough to start the engine. The moment the engine fires, the appropriate ignition setting from the base map is used.
2D and non-mapped systems Vs 3D mapped systems
After-market mapped ignition systems are now quite common, and you may wonder what advantages they offer over a conventional ignition system. A conventional ignition system is a 2D system that only takes into account engine speed and not load on the engine. It gives a constant timing that is dependent on engine rpm only. At full throttle this is acceptable, however on part throttle, economy and driveability are seriously affected. In another vein with some performance engines, the required advance may not alter in a linear manner. There may be places in the engine's speed range where required advance can fall even though rpm is rising.
Some 2D systems go part of the way towards varying the ignition timing for load by fitting a vacuum advance device which advances the ignition when vacuum in the inlet manifold is high, e.g. when load on the engine is low, but this will be crude at best. A mapped system can give precisely the right ignition advance whatever the engine speed or load. This improves the tractability of the engine dramatically as well as giving far better economy.
To appreciate the difference between a 2D and a 3D mapped ignition system you have to understand a little about combustion within your engine. When a fuel and air mixture ignites within the combustion chamber, the burning of the charge starts at the sparking plug and spreads throughout the mixture from that point. It takes a given amount of time for the whole charge in the chamber to burn, expand, and hence force the piston down the bore. This is why we have to start the ignition process before the piston reaches top-dead-center. This lead-time is called "ignition advance".
It follows that as engine revs rise and the engine turns faster there is less time for the charge in the chamber to burn hence the need to increase the ignition advance with increasing engine speed. Before the age of sophisticated electronics the ignition advance was always controlled mechanically - in the very early days by a lever mounted on the steering wheel or handlebars of the machine. The driver, or rider, altered the advance according to his best guess, going on the feel of the engine - not always too successfully!
What followed was a mechanical advance system based on a centrifugal system of weights located in the distributor. As engine speed increased, the centrifugal force acting on the weights increased and caused them to move outwards against the resistance of a couple of clockwork springs, and in doing so advancing the ignition. The springs pulled the weights back as the engine slowed again reducing the advance. A series of stops and different tension springs allowed the ignition advance progress to be controlled, or altered from one engine to another, dependent on engine speed.
But there is another factor affecting advance that needs to be taken into account - cylinder filling. The speed at which the mixture in the combustion chamber burns varies with the amount of compression that the charge is under. This in turn depends on how full the cylinder is before compression takes place. For example: on a small throttle opening at higher rpm, the cylinder will only partially fill, compared to wide-open throttle at the same engine speed. It follows that you need different ignition timings for the same engine speed, but dependent on throttle position or engine load.
With the centrifugal distributor advance systems, manufacturers often fit a vacuum advance unit. This pulls the timing to more advance when there is a high vacuum present in the inlet manifold (throttle closed or nearly so). The problem with these mechanical systems is that they are crude in operation and movement of the distributor base plate at high rpm causes timing scatter. For this reason most performance engines have the vacuum advance removed and the base plates welded up.
An EMS can control the ignition with very few moving parts; all it needs is a trigger and a load sensor of some kind. The EMS knows the load on the engine as well as the engine rpm. Since the ignition timing is mapped for each engine speed and load, the timing is at the optimum for the engine for each load condition including part throttle. This gives the best possible performance and economy whatever the throttle position. In addition since the triggering systems invariably have no physical wear points the timing stays set correctly more or less indefinitely and is maintenance free. There are other spin-offs such as rev limiting, shift light, accurate tach driving and tell-tale as well as the certainty that the timing is never likely to ‘go off’.
The benefits from a mapped system have to be experienced to be appreciated. Throttle response is razor sharp, economy is improved and tractability (especially with more radical cams) is amazing. In my own experience an engine converted from a centrifugal advance type of system to a mapped system undergoes a radical transformation.
Conversion of ignition from a non-mapped system
To convert from a normal distributor-based system to a mapped system is not as difficult as you might think. In addition to the EMS/mapped ignition unit you will need a throttle potentiometer to measure throttle angle (and therefore load) which needs to be attached to your throttle spindle, and a distributor with no advance mechanism, in place of your existing distributor. Usually most of the existing ignition system - coil, leads, plugs, distributor cap and rotor arm can be retained.
As an alternative to replacing the distributor the existing one can have the advance mechanism locked to ensure that it gives a constant signal to the EMS. This can be done by drilling through the weights and base plate and inserting a self-taper or by brazing/’MIG’ing the advance mechanism solid.
The EMS will require an electronic signal from the distributor so a points-based distributor will not do. Most post-1980 engines have electronic ignition so if your engine doesn't have an electronic distributor it is usually possible to find a later distributor for your engine, that has a magnetic reluctor or Hall effect trigger. Some later versions of your engine may well have a factory-fitted EMS which uses a Hall effect or reluctor-triggered distributor that may also not have an advance mechanism. If so this is ideal. If you cannot find a suitable replacement, then a Lumenition eye fitted in place of the points will do the trick.
The EMS will require some fairly straightforward wiring in and obviously will require a mapping session on a rolling road. Most EMS suppliers have example maps available which are ‘safe’ and will get you up and running for your trip to the rolling road.
If you don't have a map to start with then the existing curve from your mechanical distributor can be plotted using a timing light and some patience, and then programmed into the EMS. Adjustments can be made for part throttle, starting and idle and this should get you going.
Engine Mapping
Generally mapping of an engine takes place in a controlled environment where engine temperature and air temperature can be controlled or at least measured. On after-market systems the mapping is normally done using a laptop PC which is connected to the EMS via a serial cable. Software supplied by the EMS manufacturer usually allows re-mapping of the fuel and ignition requirements with various degrees of flexibility and ease of use.
The EMS is normally able to relay back to the PC all the relevant information about the engine telemetry; coolant and air temperature, rpm, load site, current timing, current fueling, Lambda reading etc. while the engine is running. For a manufacturer an engine will be installed on a test rig which can control and monitor the engine's performance and environment exactly.
For an already installed engine, mapping is usually done on a rolling road which has a ‘pegging’ facility that can hold the rollers at a fixed speed regardless of input torque. A rolling road is a set of rollers on which a vehicle can simulate driving. The rollers are attached to a ‘brake’ that can measure the turning force applied to them and the roller speed. Using these two pieces of information, the power applied to the rollers by the car's driven wheels can be measured. Generally an engine will produce maximum torque for any given speed and load when the fueling and timing are at their optimum.
Starting up
When there is no existing map, the first trick is to get the engine started. The ignition is set to 20 degrees or so at speed sites 0 and 1 at load site 0. Fuel is added at these sites by increasing the fuel number in the map dynamically as the engine is cranked until the engine fires. If the engine temperature is very low then a degree of correction is applied to the map to enable the engine to start. Once started the engine is allowed to warm up using only the first load and speed positions.
If the engine starts to die the fueling is altered to ‘clean up’ the running. It may be that the throttle and balance need adjusting for the engine to run. This is generally done before mapping commences. By the time the engine is hot, the fueling at that load/speed site will be trimmed to almost correct. This fuel setting can then be used as a basis for all the speed sites at that particular engine load. This will be sufficient as a starting point and will allow the engine to run at those engine speeds.
The next step is to trim the idle fueling and ignition until the idle is at the desired engine speed and is reasonably clean. This is because mapping involves a lot of stopping and starting of the engine. If the idle settings are wrong the battery will be quickly flattened. Quite often the timing at the speed site just above idle is set to a very low figure which stops the engine from racing when at idle. If the engine speed rises the timing drops back and causes the speed to drop again. Similarly at the speed site below idle the timing is set quite high to ‘kick’ the engine if the idle speed drops. Once this is done the mapping can start in earnest.
The mapping process
The rolling road is set to hold at a particular rpm by driving the car on the rollers in a high gear until that rpm is reached, and then ‘pegging’ the rollers. By applying the throttle the operator can hold the engine against the rollers pegged position so that the engine speed and throttle position is constant. At this point the fueling is adjusted until the Lambda reading indicates that the mixture is stichomythic (chemically correct).
If at any stage during this adjustment, pinking is heard then the operator will back off the timing. Then the operator will adjust the timing until the rollers indicate maximum torque while he listens carefully for pinking. If the torque starts to fall or the operator can hear pinking then the engine is over-advanced and he will retard the timing.
At the point of maximum torque the operator will back off the timing until just before torque starts to fall. This means the engine will be set at the minimum advance for maximum efficiency or minimum best timing.
Use of this technique minimizes the possibility of pinking or detonation in operation. Once a particular engine speed and load site has been mapped in this way the fueling and ignition values can be extrapolated to all successive speed sites for this particular engine load as a starting point. Even though these will not be correct they will be near enough to allow the engine to run. The operator will then continue for every load site at this engine speed.
This process is repeated for each successive speed and load site (or at least those which can be reached) until the mapping process is complete. Once the overall mapping is done, attention can be paid to the adjustments or corrections to the map, namely cranking, acceleration/deceleration fueling and cold start adjustment. The most difficult of these to gauge is the cold-start adjustment since the engine will now be stinking hot. Often the owner will need to adjust these to give the best starting although the operator can usually supply some reasonable estimates for the cold start adjustment. It is important to make sure that the maps which have just been constructed are saved onto the hard disk. It is the operator’s responsibility to make sure that the map is extracted from the EMS and then saved.
It is during this mapping that the quality of the software has a part to play - ease of use and intuitive display of information is critical if the mapping is to proceed safely and in a timely manner.
When the engine has been mapped it is quite interesting to examine the maps. Normally the map information (after a little massaging) can be imported into Excel or a similar graphing program and plotted as a surface contour. Some EMS (such as the Emerald M3D and GEMS system) have a graphical display built in to allow the maps to be viewed as a surface contour or wire-frame graph. Visualizing the maps in this way gives a much better and clearer picture of the engine's fuel requirements and helps to iron out any ‘glitches’ in the maps.
Generally fuel values are very small on part throttle and grow considerably when the throttle is opened (since more air is inducted to the engine). The peaks on the fuel map are usually where the peaks in the torque curve are and in most cases fuel drops off above peak torque even though horsepower may be rising. This is because cylinder filling or Volumetric Efficiency is lower past peak torque. Although the engine is consuming more fuel, it is using less per revolution since it consuming less air per revolution.
Often the operator will provide a no-fuel position at the maximum load site at speed site zero. This is provided to clear out a flooded engine. Then to clear the engine of fuel it is necessary to open the throttle to its maximum and then crank. Since cold start and cranking fueling adjustments are percentage corrections to the fuel map, when applied to a zero fuel setting they will also be zero.
Ignition timing maps look rather different. At part throttle ignition timing is generally much higher, often reaching more than 45 degrees since partially full cylinders burn much more slowly and require more advance. It is this part throttle mapping which is critical to the flexibility of the engine, especially when off-cam. Around idle the timing numbers will be quite large to sustain a rock-steady idle and will fall back rapidly above idle to stop the engine from racing. Peak timing at wide open throttle is normally reached at around 3500-4000rpm and depending on engine type a further small increase may be required above 7500rpm.
Conversion to throttle bodies/EMS from carbs or plenum
Conversion of an existing carburetor or plenum-based installation to throttle body injection is relatively straightforward provided that you fully understand what is required for the installation. If you are replacing carbs then you will need the following parts:
An EMS
A baffled fuel tank
A high-pressure injection fuel pump
A fuel pressure regulator
Some injectors of the right capacity
The appropriate ‘snap-on’ connectors for the injectors' wiring
A configuration of throttle bodies (optionally with manifold)
A throttle linkage
A throttle position sensor (usually supplied with the EMS)
A coolant temperature sensor (usually supplied with the EMS)
An air temperature sensor (usually supplied with the EMS)
A fuel rail (often included with the throttle bodies)
Air horns and air filter
Plenty of high-pressure rubber fuel hose and clips
Some 8mm fuel pipe
Patience and a sense of humor.
If you are converting from an existing plenum-based injection system, then you may not need to convert your fuel tank and can usually retain the fuel pump, injectors, fuel rail and pressure regulator. Quite often the throttle pot and coolant sensor are also re-usable especially with plug-compatible EMS replacements.
Fuel Tank
The main factor to consider when converting from carburetors to injection is the fuel delivery system. The fuel tank is the first link in the fuel delivery chain. A normal un-baffled fuel tank is not suitable for an injected engine since under the influence of the various ‘G’ forces encountered in a moving vehicle, the fuel can move away from the tank pick-up and cause the fuel pump to suck air. With a carburetor-based system the carb has a float chamber from which the fuel can be drawn if the pump supply dries up. An injection system on the other hand has no such reservoir. If the supply of fuel to the pump dries up then the engine will cut out due to lack of fuel. This is exacerbated by the fact that the fuel pump runs all the time with an injection system, with surplus fuel being diverted back to the tank via the pressure regulator.
There are two ways of counteracting this fuel starvation. One way is to compartmentalize the tank, i.e. build a compartment around the pump's outlet which is fluid-tight and use one-way valves that allow fuel in to the compartment but not out again. This keeps the fuel in the area of the pump outlet, which also can be supplemented by fitting a small conventional auxiliary pump that can shunt fuel from the opposite end of the tank to counteract the effects of fuel-surge. The other way is to use a fuel reservoir or surge-pot that holds a liter or so of fuel, and supplies the pump regardless of the fuel situation in the tank. This is fed by a small pump from the tank or by gravity, and is sufficient for several seconds of engine activity. Ensuring that the fuel returned from the pressure regulator is directed at the pump outlet can also minimize the effects of surge in the fuel tank.
You cannot convert to injection and not pay attention to your fuel tank - it absolutely must be baffled and compartmentalized, or fitted with a surge-pot.
Fuel Pump, lines and regulator
An injection fuel pump is very different to a conventional fuel pump used to supply carburetors. Firstly it runs all the time and does not ‘stall’ as a conventional pump does when the float chambers are full. It also supplies fuel at a much higher pressure than a normal pump at around 80-100psi compared with 5-6psi. It is also essential that the pump be fed by gravity, since an injection pump is designed as a ‘blow’ pump rather than a ‘suck’ pump. The requirement to gravity feed the pump normally means that it has to be mounted underneath and adjacent to the fuel tank, so a fused power supply is required to be run into that area. Since the fuel is continuously delivered and returned to the tank, two fuel pipes are required - a supply pipe and a return pipe. Normally the existing fuel line can be used as the return pipe with a new line laid in for the supply. When plumbing in the pump it is absolutely essential that high-pressure fuel pipe is used. Normal rubber hose will not do. It will burst and cause a fire hazard. Ensure that you only use properly rated hose capable of withstanding in excess of 60psi. The inlet to the pump is normally 12mm internal size, so the spur from the tank must be this size also. The remainder of the fuel pipe can be 8mm copper or steel tubing. Ensure that the ends of the tube are ‘flared’ to help the integrity of any joins.
Injection pumps are noisy so make sure that you mount your pump in a cradle of some kind suspended by rubber cotton reels or wrap it in some sound deadening material before mounting. Don’t take chances with the pump - it must be properly insulated and leak free.
Injection pumps require that the fuel be filtered before it reaches the pump. In some cases this is not easy to arrange. However any dirt or rubbish entering the pump can and will cause it to lock solid and render it permanently inoperable or damaged. Where space is limited, a fine wire-mesh screen can be used in the inlet to the pump provided that it is fitted in such a way that it cannot enter the pump. This will screen any reasonably sized particles. If you are using this method ensure you clean/change the screen regularly and fit a proper fuel filter following the pump.
There are plenty of injection pumps to be found in the scrap yards - most vehicles post-1989 are fitted with injection systems and are a good source of pumps and injectors. If you select a vehicle with a suitably sized engine then the pump should be up to the job. It's likely that the injectors won't be far out either. It is quite possible that the fuel pressure regulator might be suitable assuming that it is not integrated with the fuel rail. My pump injectors and pressure regulator came from a broken Sierra Cosworth. Alternatively you can source the pump from a motor factor or specialized supplier.
Induction system
If you already have twin Weber's or Dellorto's fitted to your engine then the obvious choice of induction system is a flange compatible throttle body kit such as the TB throttle bodies from Jenvey. These will bolt on directly in place of the similar styled DCOE's or DHLA's. If you have IDA or IDF Weber's then the TF bodies are flange compatible. If your engine is not already equipped with dual side draught/down draught carbs then you must make the appropriate selection of either dual or single throttle bodies with an appropriate manifold and air horns/filters. I have had some success having back-plates made to take the dual ITG filter on the end of a set of air horns attached to either dual or single throttle bodies. This makes a nice neat installation. If you are using the parts retained from a carburetor set-up then you can re-use the filters and back-plates. If you cannot obtain a suitable manifold for your engine then it is possible to fabricate one.
Some throttle bodies will bolt directly to the cylinder head notably some of the range produced by Jenvey.
If you are upgrading from a plenum based system then you may find that you can re-use the fuel rail, injectors, pressure regulator and throttle position sensor. This will save money and aggravation. Some ingenuity may be required in the fabrication of brackets to attach the OEM components to the new throttle bodies but it is not a difficult task.
When buying the throttle bodies you must also purchase a throttle linkage since the type used on twin side draught carburetors is not suitable and cannot be used. Generally throttle body kits come complete with fuel rails that are designed to take the standard Bosch type of injector.
Air horns are generally necessary and the main limiting factor for length is the space available on the inlet side of the engine. Measure carefully here to ensure that what you are buying will fit.
The throttle potentiometer is normally fitted to the end of the spindle on one of the throttle bodies, ensure that it is fitted so that it is opening and not closing, e.g. against the spring tension.
Plumbing in
After running the fuel line as close as possible to the end of the fuel rail, the plumbing in is a simple task. If you are retaining an existing fuel rail arrangement then it should simply be a matter of bolting on the rail and connecting as before. When fitting a new rail it is important to ensure that the injectors are properly clipped to the rail and that the rail when fitted holds the injectors firmly into their position in the inlet manifold or throttle body pockets. The fuel supply should be connected to one end of the fuel rail with the pressure regulator connected to the other. The outlet of the pressure regulator is then connected to the fuel tank return pipe. The return pipe should dump its fuel as close as possible to the pump outlet in the tank.
Wiring
Generally the only things to connect are the fuel pump which requires a fused supply that is switched by the ignition, the throttle potentiometer which is connected to the EMS, the coolant and air temperature senders that are again connected to the EMS and the injectors themselves. Finding a place for the coolant temperature sender is not always easy but often it is possible to drill and tap an existing boss somewhere on the engine which must be the engine side of the thermostat, preferably in the head. The air temperature sender should be mounted as near to the inlet trumpets as possible.
Depending on the type of injection - batched, grouped or sequential, the injectors may be wired in parallel or in series. Follow the instructions which come with the EMS to make sure that you do this correctly. If you need the snap-on connectors for the injectors, a trip to the scrap yard is called for. Make sure you get plenty of wire with the connectors and while you are there look for the connectors which clip on to the coolant temperature sender as well.
It is a good idea to bolt the throttle bodies to a dummy manifold (a piece of angle iron suitably drilled with a few correctly spaced holes will do) in order to make the injector loom and fit and adapt the throttle linkage and other ancillaries. Doing this while the bodies are not attached to the car is much more convenient as it makes the set-up more accessible. Any problems that arise with linkages, air horns, wiring etc. can be much more easily solved. Depending on resistance some injectors will need a resistor in series in order for the EMS to fire them correctly. Ensure that this is mounted and connected correctly.
When this has all been fitted satisfactorily, all that remains is to power on the pump and ensure that it is circulating fuel before starting the mapping process.
Sample surface map contours for injection/ignition
Below are a sample ignition and injection map from my EMS presented as surface contours. When visualized in this way it is much clearer what is going on.
Note the relatively high advance at idle which is used to give a rock-steady tick-over and the dip in timing following the idle position which causes the engine to dip back if the idle gets too fast. Note also the extra advance on part throttle throughout the range and the small dip in the timing at 3500rpm where, although the rpm is higher, the timing is less than at 2500 and 3000rpm.
It is clear to see where peak torque is on the engine from the injection map. The large bump on the fuel map is at 6500rpm. This is where cylinder filling is best and therefore is the point of maximum fueling and maximum torque.
You can return to the Topics menu by clicking here
 

|