How to adjust your valves properly.
First, you need to determine if you have solid lifters or hydraulic lifters. Solid lifters were commonly used on the early 144/170ci motors, while hydraulic lifters were used on the later 144/170ci and all 200/250ci engines. However, this is only a rule of thumb and may vary depending on the model type. For example; a '64 Falcon 170ci came with hydraulic lifters, while the '64 Ranchero 170ci had solid lifters. If your not sure, grab a flashlight and look at the top of the lifters. Solid lifters will have a "C" clip, while hydraulic lifters have a wire clip (see photo below).
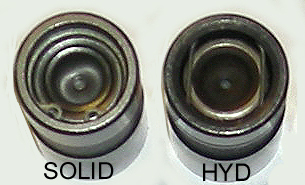 |
|
Once you've finished rebuilding a motor, and/or the cylinder head, you'll need to adjust the valves prior to starting up the motor for the very first time. It's easier if you leave the spark plugs out while your doing the initial adjustment, as this will make it much easier to turn the engine over.
If you have hydraulic lifters, the initial adjustment should be done before you prime the oil pump, as the lifters need to be fully collapsed. You can check them by using a pushrod, and pressing down on the center plunger until it bottoms out. Make sure you push long enough and hard enough to get all of the oil out, and be sure to check every lifter.
Start by rotating the crank clockwise, while your watching the valves in the #1 cylinder. When the exhaust valve begins to move downward, stop rotating the motor and adjust the intake valve to the proper lash. Next, continue rotating the engine clockwise, until the intake valve reaches maximum lift and is almost all the way back down, then stop and adjust the exhaust valve. Continue adjusting the valves in each cylinder, until they are all adjusted to the proper lash. For hydraulic lifters, you want to snug down the adjuster just enough to keep the pushrod from spinning (using your finger tips). Then tighten them 1/4 turn more. For solid lifters, do exactly the same thing, but instead of tightening 1/4 turn, loosen them 1/4 turn. This should get you pretty close, at least until you can do the final adjustment.
Final Adjustment for Hydraulic Lifters |
Final valve adjustments should be done on an engine that has been warmed up. Make sure to let it cool off sufficiently so that you don't burn your fingers while rotating
the pushrods. It is also a good idea to place a drop cloth or oil pan under the car/engine
to prevent oil drips on the floor. Make sure you disconnect the coil wire before you do anything to make sure the motor won't start accidentally. Some guys prefer to remove all the plugs too, so the engine is easier to rotate during the procedure. Make sure you mark the plug wires before you disconnect them, so you don't mix up the firing order when you reinstall them.
First, rotate the engine until the #1 cylinder is on TDC, just after the compression stroke (you can feel the compressed air by putting your finger over the
spark plug hole). Now you can adjust the following valves:
#1 intake - #1 exhaust - #2 intake - #3 exhaust - #4 intake - #5 exhaust
Next, rotate the engine until the #6 cylinder is on TDC, just after it's compression stroke (one full revolution of the crank shaft). Now adjust the remainder
of the valves:
#2 exhaust - #3 intake - #4 exhaust - #5 intake - #6 intake - #6 exhaust
Adjust the valves by backing off the adjuster so that the pushrod can be easily rotated between your thumb and forefinger. Then slowly tighten the adjuster until you can no longer rotate the pushrod. Tighten the adjuster an additional 1/4-1/2 turn for the proper preload on the hydraulic lifter. We normally recommend 1/2 turn for a daily driver, and 1/4 turn for a performance motor with a higher rpm range.
Final Adjustment for Solid Lifters |
While solid lifter valve adjustments must be made as accurately as possible, it is better to
have the valve adjustment slightly loose, rather than slightly tight, as a burned valve may result from overly tight adjustments. Look in your engine manual to determine the proper valve lash for your motor. If you can't find it, they were commonly set at .018 thousands, but this lash should only be used as a very last resort.
1. Start the engine and let it run until it has reached operating temperature.
2. Remove the valve cover and gasket.
3. With the engine idling, adjust the valve lash using a step-type feeler gauge. This type of feeler gauge is sometimes more commonly known as a "go-no go" type feeler gauge. The proper clearance is reached when the smaller step on the gauge blade will pass through the gap while the larger step on the same blade will not pass thought the gap.
Pass the proper size gauge blade between the valve stem and the rocker arm. If the clearance is correct, move on to the next valve. If the clearance is in need of adjustment, turn the adjusting screw on the opposite end of the rocker arm with a wrench until the proper clearance is reached. Turn the screw clockwise to decrease the clearance and counterclockwise to increase the clearance. Use the procedure for all of the valves.
4. Re-install the valve cover after you finish adjusting the valves.
Other related articles:
Understanding Lobe Centers - Static vrs Dynamic Compression
Cam Installation Tips - Adjusting Your Valves