This article is currently under construction. This is only a rough draft, which still needs to be edited and checked for errors.
This article was complied from numerous articles and resources found on the internet, as well as our own experiences. The purpose of this article is to cover the basics things you'll need to know to make your Weber carbs run properly. For more detailed information, please refer to the “Weber Factory Tuning Manual” which is published by Haynes.
Triple Weber carbs offer an unparalleled experience, with throttle response and mid-range torque being second to none. The first thing most people notice when they go to multiple Weber’s, beyond performance and appearance, is the ability to finely tune, or dial in the induction system.
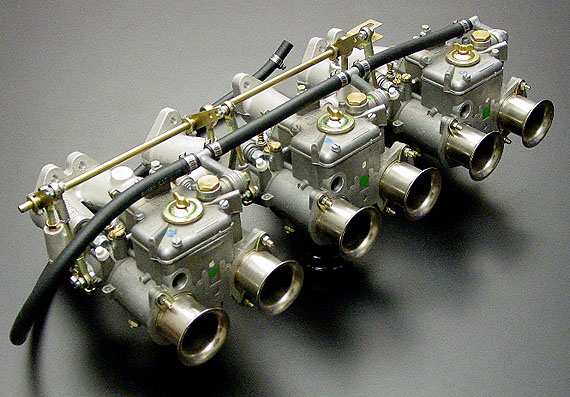 |
Weber carburetors were designed to be totally adaptable, to any size engine, for any purpose, at any altitude. There is a natural tendency for Weber-carbureted engines to idle smoother, particularly with a hot camshaft that may have idled roughly beforehand. Weber carbs also have a tendency to suppress detonation or pinging caused by uneven fuel distribution, which is a common characteristic of conventional log manifolds that distribute fuel from a central plenum chamber. This uneven fuel distribution causes the outer two cylinders to run lean, creating excessive cylinder heat which can lead to pre-ignition and detonation. The only way to eliminate these lean cylinders, is to distribute the fuel perfectly and evenly, to each and every cylinder.
The only way one can achieve perfect fuel distribution is by using multiple carbs or fuel injection. In fact, multi-carb induction systems respond to the gas pedal in a manor very similar to fuel injection. This is because both systems normally have short isolated intake runners, with a small mass of fuel/air to move when the throttle is cracked open. This is attributed to the independent-runner manifold, which does not incorporate a plenum chamber. In a typical multi-carb layout, one barrel directly feeds each cylinder, without any intercommunication between the barrels or cylinders. This "isolated runner" design ensures that each cylinder is fed exactly the same as the next, without any chance of charge-robbing or over-feeding any one cylinder. What you are doing, in effect, is separately tuning each cylinder, or carb, to achieve perfect fuel distribution.
Even with all their advantages, multi-carb induction systems are not for everyone. The reason for this is usually two fold, higher cost and/or increased complexity (or should we say fear). Lets discuss cost first. This type of induction unit represents a sizeable investment. In order to install triple Weber's on a small six, you'll need to purchase an OZ 250-2V cylinder head, or our aluminum cylinder head. You also need to purchase three side-draft carbs, air filters, linkage, fuel pumps and/or regulators, fuel lines, gauges, and an appropriate
The price of opening up a box and pulling out a Weber unit with all the right pieces and associated hardware will run you about $4,200.00. But consider that all things are relative, and that you get what you pay for. In the end, it all boils down to what you want your car to represent. As they say, "the fun's in the driving". Weber carburetion offers much more than something that's exciting to look at. Every time you take that machine of yours down the road, the throttle response, quick acceleration and overall flexibility are constant reminders of what you've spent your money on: the ultimate carburetion system.
The reason Weber's are so well-suited to road racing is that they make so much more power over the entire rpm range. This is a perfect characteristic for street-driven cars. When you think about it, you spend very little time at the upper end near redline, like the drag cars do. And while making all that midrange power, what you also have is an engine that revs really fast. It takes on a whole different personality.
Remember, you're not asking that cylinder to gulp the mixture from a big plenum area; that's a lot of mass, by comparison. The only air mass to move is what's in one short runner. The main difference between fuel injection and Weber carburetion is that one relies on fuel being injected under very high pressure, while the other responds to the needs of the engine via the depression principle (air velocity in the carburetor based on its venture size). However, this carburetor was intended for serious tuners and performance enthusiasts who want the most out of their engine and know how to work with them.
Diagrams |
|
|
|
|
32/36 DGV |
38/38 DGS |
DCOE |
In order to get driveability, throttle response, and lots of torque from a Weber carb, the choke size (cfm) is the first consideration. It’s the heart of the matter. How big is the motor, what's the compression ratio, and what are you going to do with it? Once the correct size choke has been selected for your application, the jetting for all the circuits can be calculated around that choke size. If you change the chokes (which changes the cfm), you must also change the jetting.
For the sake of simplicity, let's look at the Weber carburetor as having three basic circuits: the idle circuit, the accelerator pump circuit, and the main circuit.
THE IDLE CIRCUIT
The idle circuit is comprised of two components, the idle jet and the idle jet carrier. With these two pieces, the tuner can meter the right proportion of fuel and air at idle — and during low rpm operation. The idle mixture is delivered as a pre-mixed fuel/air mixture, and the total volume is regulated with the idle mixture screw located on the lower part of each carburetor barrel.
If the idle circuit is correctly jetted, the mixture screws on an independent runner Weber system are usually never more than 1-1/2 turns out from closed (in the old days it was 3/4 turn, but nowadays, the oxygenates and ethanol in our gas requires extra richness). So if you have to open the mixture screws more than that, it’s time to heavy-up the idle circuit. So even though it idles okay, going more than 1-1/2 turns out tells you the jet is basically lean (and you're usually going to have a driveability problem), which brings us to the next part of the idle jet's function…
The idle jets in the Weber aren’t just for idling. The idle circuit is actually the low-speed circuit and must carry the engine all the way up to about 2,500 rpm, where the transition to the main circuit take place. That means if you don't drive over 2500 rpm, you're only running on the idle jets. After 2500 rpm or so, the idle circuit is entirely bypassed and no longer has anything to say. So, if you have a driveability issue, like a stumble, or rough spot that "goes away" after about 2500 rpm, that tells you to spend time tweaking the idle circuit. Or maybe the opposite is true. Either way, the two circuits are completely separate, so isolating the problem is fairly simple.
As mentioned above, one the most common "gremlins" with Weber carburetors is a seemingly incurable and very annoying flat spot shows up anywhere between 2,200-2,800 rpm. This condition is generally caused by one of two things. Either the wrong emulsion tube is in the carburetor, which is causing a rich stumble due to an under-emulsified mixture at that particular rpm range, or the idle circuit is falling off too early and not carrying the engine up to the point where the main circuit takes over. When that happens, it leaves a "lean hole" that feels like a stumble.
In the case of the wrong emulsion tube, there are really only a few that work really. If you aren't using one of them, it’s a big part of the problem. If the flat spot is still there even with the correct emulsion tube, then you'll need to richen up the idle circuit. This is sometimes a tricky area, because the first thing you want to do is throw in a bigger idle jet, but sometimes playing with air bleeds, mixture screws, or choke sizes can accomplish the same thing while sticking with the original jet size. A little experience comes in handy here.
Seeking some sound advice can save a lot of time and aggravation. Driveability problems can be solved with a little tuning on your own or by relating the symptoms to someone who is knowledgeable enough to help you. Remember, these carburetors will do just about anything you want them to, as long as you know how to work with the symptoms.
ACCELERATOR PUMP CIRCUIT
The accelerator pump circuit, just like on any carburetor, is responsible for eliminating "bog" and making a passing maneuver without a hesitation or stumble. This circuit also has two basic calibration elements: the pump exhaust valve and the pump jet. The pump exhaust is a bypass valve located in the bottom of the float bowl. This is the piece that regulates how much fuel you want to make available when you need that pump shot. Putting a bigger bypass hole in the valve allows more fuel to bleed back into the float bowl instead of out of the shooters. The smaller the hole, the more fuel you're making available. You can even put in a "closed" bypass for drag racing, when you need all the gas you can get. The duration of the pump shot is varied by installing a larger or smaller pump jet (shooter). Larger pump jets give a heavy blast over a short period, while the smaller ones will give a finer, longer-duration shot.
THE MAIN CIRCUIT
The main circuit is the easy one. This is where you make your power. This circuit has three primary elements you should concern yourself with: the main jet itself, the emulsion tube, and the air corrector. You probably thought the main jet was all there is. In a conventional carburetor, you’d be right. But these are not ’t conventional carburetors.
The main jet is stuck into the bottom of the emulsion tube and sits in fuel. As the carburetor begins to work, the main jet meters the amount of fuel allowed to pass through it and up into the emulsion tube. Air enters the top of the emulsion tube through the air corrector which meters the amount of air to be mixed with the fuel coming in from the main jet. The air blows out of the emulsion tube through a series of holes along its length and aerates the fuel as it rises up the well around the tube. This emulsified mixture is then sucked out of the main delivery nozzle as the velocity in the carburetor increases. This usually occurs by 2500 rpm or so, and once that main circuit comes on, you’re off like a rocket.
Tuning the main circuit for maximum power is something that can be done by a series of road tests and a handful of jets. The simple rule of thumb for jetting Weber carburetors is, if you want to implement a change over the entire rpm range, you play with the main jet. If you want to change the way the car feels at the high end, that's more the domain of the air corrector. Also, you should keep in mind that the air corrector is a finer adjustment than the main jet. One step upward in the main jet (richer) equals about the same as three steps down on the air (less air: richer).
A change of air corrector would be appropriate if the engine pulls strong to 5,000 rpm and then lays down before the redline. In that case, I’d drop the air corrector about three sizes, and you'd probably be able to buzz the engine right up to 7,000 rpm. If it feels sour all the way up, then I’d go one or two sizes heavier on the mains only. It’s not rocket science. So what’s so hard about jetting Weber's? Obviously, nothing if you understand how they work.
TUNING AND MAINTENANCE
A Weber carburetion system must be synchronized so each carburetor is doing exactly the same as the rest. The synchronization procedure is done with a Unisyn or a Synchromer (a necessary tool that should always be supplied with any new V8 Weber system). It can either be a breeze or a nightmare, depending on whether you have a well-designed linkage system or not. The secret to a good linkage setup is that it must allow independent adjustment of each carburetor without affecting all the rest as you go through the procedure, and there should be a "master idle speed screw" to raise or lower the rpm of the engine without disturbing any of the settings of the individual carburetors. The master idle speed screw acts on the entire linkage system as a whole. So, if someone tells you Weber's are absolutely impossible to synchronize, question the linkage. Chances are, it's a mess and it's fighting itself.
The final idle mixture adjustment for each barrel is a simple adjustment performed by ear, but for some reason, a lot of people feel intimidated because there are three carburetors. It's done exactly the same way you adjust the mixture on a two barrel or four barrel carb, except with Weber's you can listen to each cylinder, one at a time. So, while it may take you three times longer, it's not three times harder.
Each mixture screw, as it is turned, will have a noticeable effect on engine rpm; the wrong setting will cause the cylinder to "go away", almost like if you pulled a plug wire. No matter how hard you try, you can't mess this up if you remember one thing: always start from scratch with the screw seated, and then come out between 3/4 and 1-1/2 turns. That’s the correct starting point. From there, turn the screw 1/8 of a turn either way and listen carefully. This method will always get you out of the woods if you get lost. If the mixture screws want to be out more than 1-1/2 turns, the jetting should be made richer.
Once the unit is synchronized and the idle mixtures are dialed-in to give you the smoothest possible idle, you can hang up your synchronizing tool and screwdriver, because now it's set, and when it's set, it's SET. They will not suddenly "go out" on you and become unsynchronized. For some reason, it’s one of the stories we’ve all heard a hundred times…that they constantly go out of adjustment. That is absolutely not true; they do not.
CAMSHAFT LOBE CENTERS
Any cam is fine as long as you pay attention to the lobe separation angle. A 110-112 degree lobe separation is ideal for Weber's. I generally discourage the use of anything tighter, like 108, or 106. The problem with a lot of overlap is that it causes "reversion" (reverse pulses) from the exhaust stroke that have nowhere to go but up into the carburetor. This disturbs high rpm airflow and causes the engine to think it's too lean at high rpm’s. Without a plenum, the manifold flow columns are pushed backward, up into the carburetors.
MISC NOTES
Your float setting is critical beyond words. We need to confirm that they are all set to factory specs. If that remains an unknown, re-jetting won't correct a driveability, leaking, or richness problem. In addition, your ignition timing is a huge component, and if set wrong, can create serious heat in the block contribute to percolation of fuel, and make the engine sluggish and rough, so the timing must also be set properly. Lastly, your fuel pressure and the type of regulator you are running are extremely important.
|